Rising input costs and ongoing legislation restricting the availability of chemicals on environmental grounds have brought the accuracy of crop spraying applications sharply into focus for manufacturers and operators alike.
Pulse width modulation (PWM) technology, which uses pulsing solenoids to control individual spray nozzle valves and alter spray volume and flow with increased precision, is designed to offer greater precision, cutting chemical costs and mitigating the effects of chemicals on the environment.
Its operation is governed by the speed at which the solenoid can be switched on/off, expressed in Hz, while the Duty Cycle (DC) – the length of time the valve remains open during each cycle – determines the amount of liquid released.
Higher duty cycles maintain the chosen application rate at lower pressure, so the droplet spectrum can be maintained without having to change the nozzle, enabling the sprayer to be operated at a wide range of speeds and for variable rate applications.
The ability to control DC also provides turn compensation – increasing application rate at the sprayer boom end and decreasing it towards the centre of the boom to compensate for over- or under-dosing caused by the difference in speed at which the centre and outside of the boom travel around a turn.
Spray applications are more uniform and controllable, safeguarding non-target vegetation and allowing use in a greater range of conditions, and an increasing number of sprayer manufacturers are offering in-house or proprietary PWM systems on their machines.
John Deere’s ExactApply® spray technology
John Deere’s ExactApply system combines the ability to change spray nozzles manually from the cab or automatically depending on application rate and speed with the use of PWM technology up to 30Hz.
Each nozzle is controlled individually via GPS-based section control and with PWM enabled, turn compensation ensures that application rates remain consistent across the full boom width when turning the sprayer.
John Deere Product Sales Specialist Mark James comments that while PWM itself does not necessarily cut costs, individual nozzle control can save 3-5% by minimising overlaps.
“Where PWM comes into its own is by increasing the efficacy of the products being applied, which has the potential to boost yield. Turn compensation gives even application of the required spray quality across the field, and ensures that areas around poles or trees get the right amount of chemical, combating black-grass or
disease which often take hold in these areas.”
He adds that another key benefit of PWM is the ability to choose the precise droplet size for a particular task.
“It gives flexibility without having to get out and change nozzles, improving timeliness.”
Mr James points out that choosing nozzles is straightforward, using the selection chart from nozzle partner Hypro.
“There’s plenty of choice of nozzle to achieve the droplet size required, and you don’t need air inclusion nozzles to reduce drift. Operators do need a different approach to spraying, but once they have taken that on board, the actual operation of the sprayer is far simpler.”
Capstan PinPoint technology – individual nozzle control
Topeka, Kansas electronics specialist CapstanAG™ has been developing PWM technology since 1998 and is currently trialling Capstan PinPoint III, the latest version of its OEM-fit PWM system which is available through a number of manufacturers including the UK’s Bateman Sprayers and Sands Sprayers.
New features will include ISObus VT compatibility which allows the use of a single display in the cab and Task Control capability, managing application rate control. It will also offer variable rate application per nozzle based on Task Control or maps.
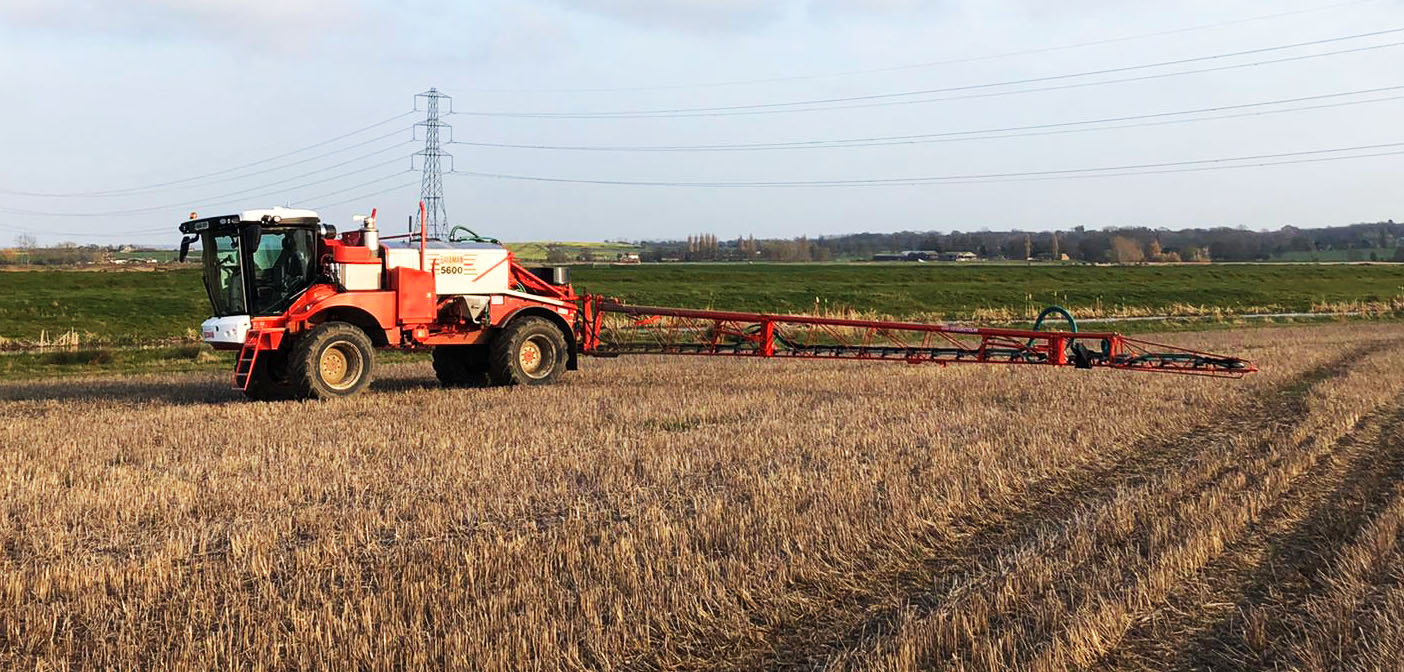
Stuart Woods has been using a Bateman RB55 sprayer with Capstan Pinpoint II PWM since January 2019, with a workload entailing 1300ha of combinable crops in Kent, England.
“The previous sprayer was up for replacement and I wanted to specify the latest technology,” he explains. “In discussion with (American sprayer expert) Tom Wolf, I discovered that on the actual sprayed area, PWM and individual nozzle control cuts over-applications by 1-3% compared with using 3m boom sections. This represented a cost saving of £5,000 a year on chemical alone for our farm.”
Added to this, the increased uniformity offered by turn compensation avoids over- or under-application on corners and turns, he points out.
“Under-dosing increases the likelihood of herbicide resistance, while overdosing can be an issue close to watercourses, risking point source contamination.”
Mr Woods says that the Capstan system is straightforward to use and adjust.
“I simply dial in the application rate and droplet size required, and where there’s a risk from drift on the headland, it’s easy to cut the pressure back and control droplet size on the move. If the wind drops, I can then increase pressure without affecting forward speed.”
He adds that it is also possible to use higher forward speeds on a long run by increasing the duty cycle and maintain pressure on a hill or a soft patch of ground where the sprayer slows down. He comments that PWM allows him to find a ‘sweet spot’ of the precise droplet size for a specific task but also affords flexibility.
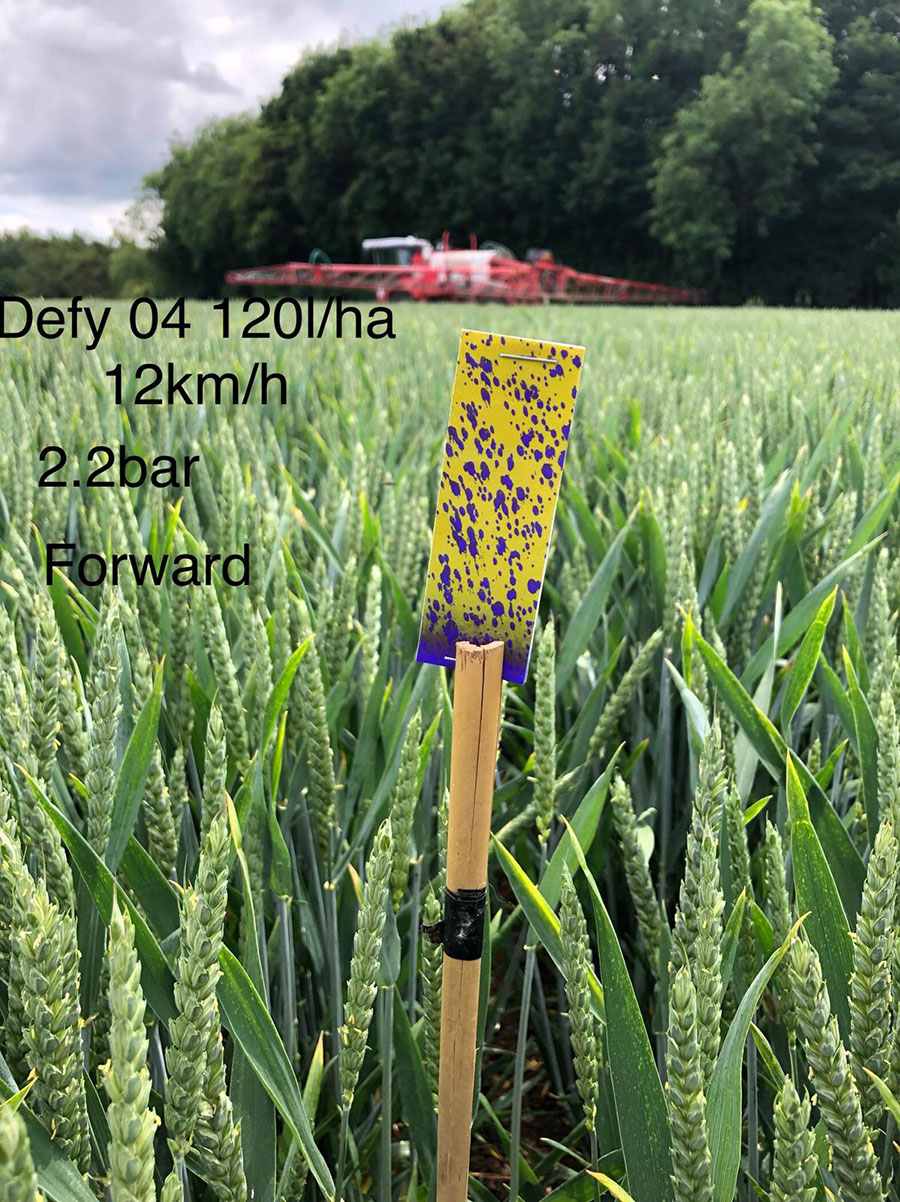
Capstan’s Pinpoint II uses its own in-cab control terminal rather than being integrated with the AgLeader screen, but Mr Woods suggests that this affords the space for the boom display icon, which allows him to easily monitor its position on turns and make adjustments to maintain the duty cycle if necessary.
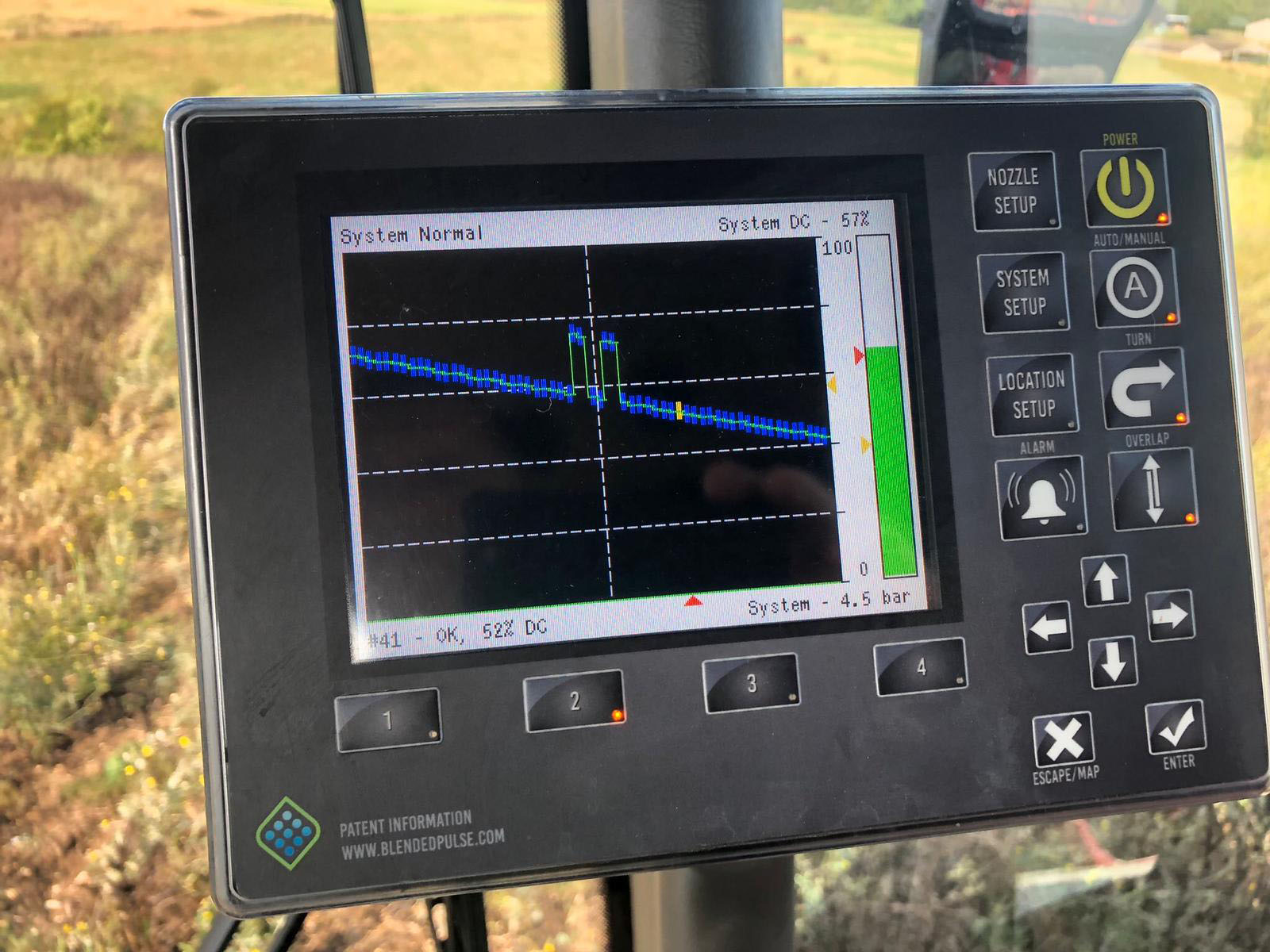
status and monitors each individual nozzle in sequence for duty cycle as well as allowing easy set up and operation.
Nozzle compatibility is often cited as a sticking point, but after some experimentation he has found success with the Canadian-made Wilger range.
“The air inclusion nozzles I used previously are not suitable, but pre-orifice nozzles work well and there’s a growing choice on the market. Wilger’s TipWizard app offers selection guidance – you simply enter the required rate, droplet size and speed.”
Mr Woods has also trialled variable rate fungicide applications this year, with the PWM system varying the rate without altering pressure and thus maintaining droplet size.
“It’s a more versatile way of spraying, and I find that I can work to the conditions while maintaining output, which with a large workload and unpredictable climate is highly beneficial.”